Stainless steel instrument tubing is a vital component for many processes and equipment. It is available in a wide variety of sizes, shapes, and grades to meet virtually any application need. This tube can be used in many industrial settings, including pharmaceutical manufacturing, marine equipment, and chemical processing plants. It can also be found in critical applications, such as cleanroom environments. Regardless of the environment, the tubing can withstand extreme temperatures and chemical exposure without corroding.
Choosing the right tubing for your project is essential, as the wrong material can lead to failure or poor performance. Considerations include the compatibility of the tube with the intended material, pressure requirements, and environmental conditions. It is recommended that you consult with experts and abide by industry standards to ensure the correct selection.
To select the correct tubing for your project, it is important to evaluate the dimensions of the tube. This includes the inner diameter, outer diameter, and wall thickness. In addition, you should consider the material and surface finish of the tubing. For example, stainless steel has a bright easily maintained surface and offers excellent corrosion resistance. However, other finishes may be more appropriate based on your desired aesthetics or functionality.
There are two types of stainless steel tubes – seamless and welded. Each of these constructions has unique properties that make them suitable for different applications. While they both provide excellent strength and corrosion resistance, the difference lies in their production methods. Pipes are typically welded using continuous processes while tubes are formed through the use of rolling, metal spinning, and tube milling. This alters the mechanical properties of the finished product.
As a result, the tube is more flexible than the pipe, which allows for greater maneuverability in tight spaces. Moreover, the tube is generally lighter than the pipe, which allows for easier transport and storage. Furthermore, since tubing has more stringent requirements, it is often more expensive than pipe.
Due to the increased risk of localized corrosion with 316 stainless steel tubing in offshore environments, many end users are selecting 6MO tubing for their process control tubing systems. This substitution is made to reduce the risk of corrosion and extend the lifespan of their tubing. This is achieved by implementing an adequate protective system, ensuring that the tubing is sized correctly for the environment and that it is installed according to the manufacturers’ recommendations. It is also recommended that the tubing is inspected for any defects before installation. This will allow for any issues to be identified and resolved before the tubing is exposed to the harsh marine environment. This can save a great deal of time, money, and downtime. It is worth highlighting that the cost of replacing the tubing can be much higher than the cost of the initial purchase. This cost should be taken into consideration when deciding on the correct tubing for your project. This will maximize the overall value of your investment.
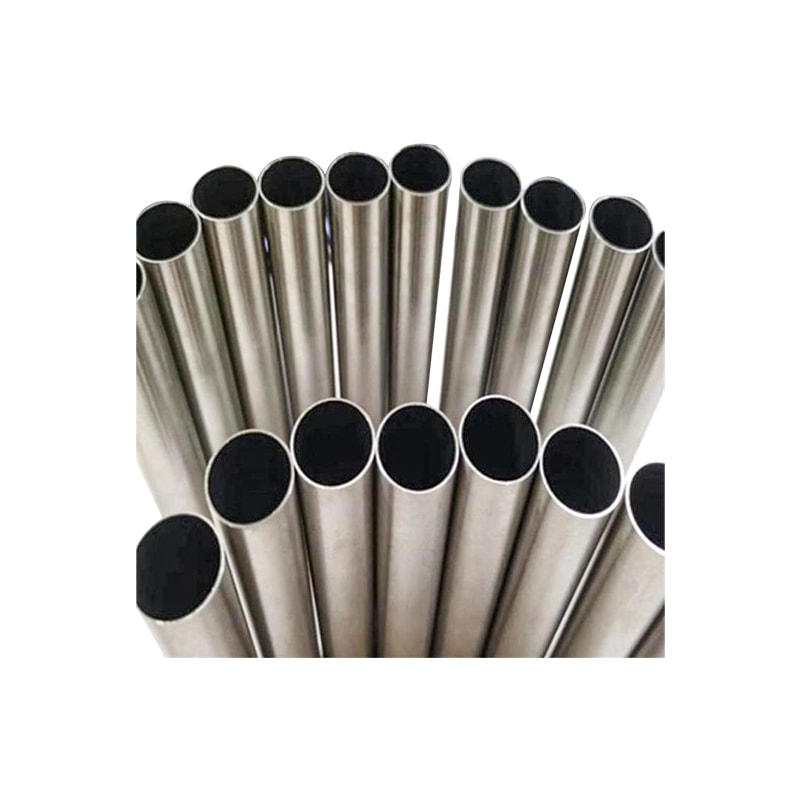
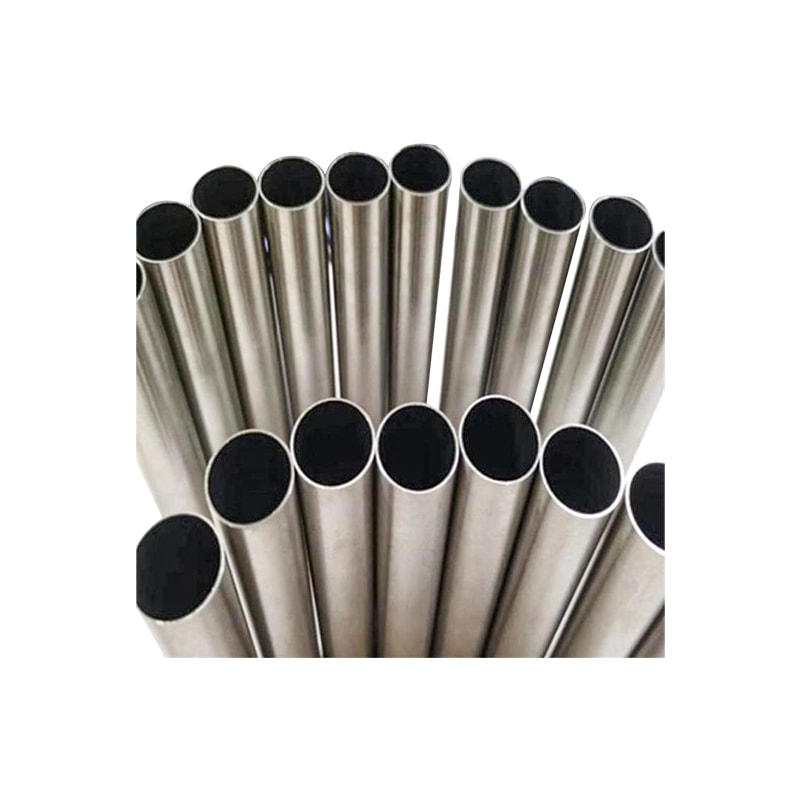