Instrumentation tube encases equipment that monitors factors such as temperature, pressure, fuel burn-up rates and density differences within nuclear reactor cores. As such it is exposed to harsh environments that can degrade many other types of pipe, so durability and corrosion resistance are key. For this reason, SS instrument tube is a popular choice amongst manufacturers and users alike. It also offers cost savings over time by lowering long-term costs from maintenance and repairs.
Typically made from 304 or 316 stainless steel, SS instrument tubing can be welded or seamless depending on the application. With a range of diameters and lengths to choose from, it is ideal for connection to a variety of pressure switches or gauges, flow monitors, valves and central piping systems. It is commonly found in ventilation, water filtration and chemical processing applications.
In order to ensure that SS instrument tubing can cope with the demands of its environment, it must be designed and manufactured accordingly. This will involve a rigorous process that will test the material to determine its capacity to withstand various forces and stress. These tests will be conducted in a laboratory or at the actual site of the installation. The results of the testing will be used to calculate the maximum allowable working pressure of the tube.
The process of manufacturing SS instrument tube is very similar to that of other stainless steel products. The raw material is supplied in coils and then formed into the desired shape. Once the tube has been shaped, it can be either welded or seamless. Welded tubes are formed by passing the strip through a welding system which will create a weld bead along the inside and outside diameters of the tube. This weld bead is then removed with the help of abrasive grinding, bead rolling or scarfing. Using these methods, a finished tube is created that has smooth surfaces and close tolerances.
As the abrasive grinding and cutting processes are eliminated, the chance of damage to the surface of the tube is significantly reduced. This will reduce the risk of leaks and rusting and increase the life cycle of the pipe. Moreover, a more consistent diameter will be maintained throughout the tube's length, which will improve the performance of the system as a whole.
While a quality SS instrument tube will offer reliable performance in all conditions, it should not be buried below the surface of the ground. This is important to prevent potential contamination of the soil and underground environment. It should also be avoided if possible because of the dangers of fire and explosion.
In addition to the quality of the SS instrument tube itself, the type of mechanically attached fittings will also impact its performance. Ideally, the tube should be fitted with a SS 310 Double-Ferrule tube fitting. This fitting provides a seal for all tubing connections and prevents potentially hazardous and costly leaks in pneumatic, hydraulic, gas, natural gas, oil & gas and cryogenic systems.
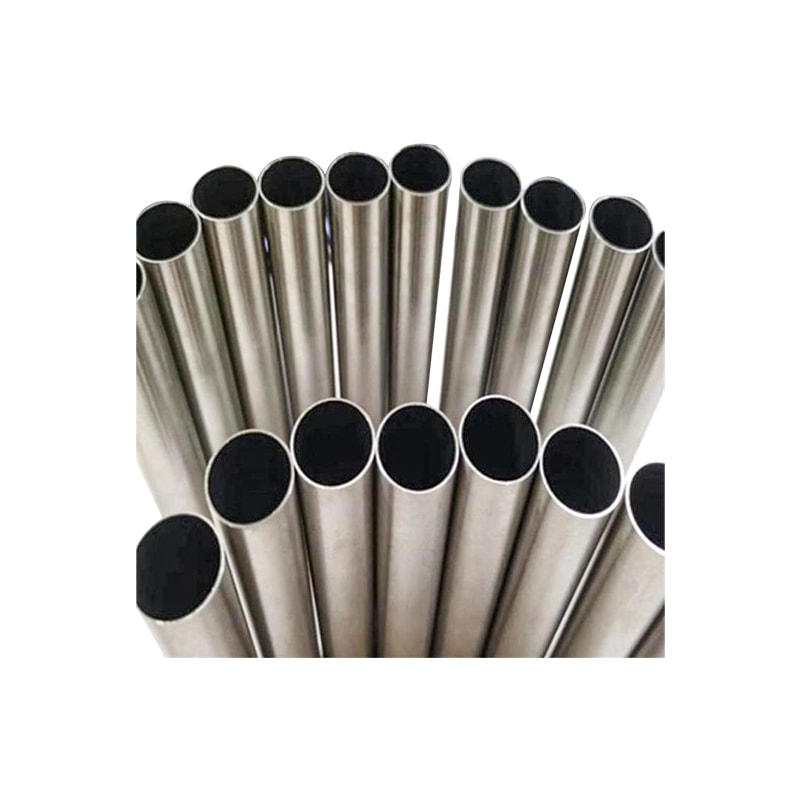