In a remarkable advancement for industries that require exceptional strength, corrosion resistance, and heat resistance, nickel alloy tubes have emerged as a game-changing solution. These specialized tubes are redefining performance and reliability across a wide range of sectors, including aerospace, oil and gas, chemical processing, and power generation.
Nickel alloy tubes stand out from conventional tubes due to their unique composition, combining nickel with other alloying elements such as chromium, molybdenum, and iron. This combination enhances the tubes' properties, making them ideal for applications that demand superior performance under extreme conditions.
One of the primary advantages of nickel alloy tubes is their outstanding corrosion resistance. These tubes exhibit exceptional resistance to various corrosive environments, including acids, alkalis, and chloride solutions. As a result, they are widely used in industries such as chemical processing and oil and gas, where exposure to corrosive substances is common. The corrosion resistance of nickel alloy tubes not only ensures the longevity of the tubes themselves but also protects the integrity of the overall system, reducing the risk of leaks or failures.
Moreover, nickel alloy tubes excel in heat resistance. They can withstand high temperatures and thermal cycling without losing their structural integrity. This attribute is particularly critical in industries such as aerospace and power generation, where components are exposed to extreme heat and temperature differentials. Nickel alloy tubes effectively maintain their mechanical strength and dimensional stability, ensuring the reliable performance of critical systems even under challenging conditions.
The exceptional mechanical properties of nickel alloy tubes make them highly reliable in demanding applications. These tubes possess excellent strength, toughness, and fatigue resistance, allowing them to withstand high pressure, vibrations, and mechanical stresses. Industries such as oil and gas exploration and production, where reliability is paramount, benefit greatly from the superior performance of nickel alloy tubes.
Furthermore, nickel alloy tubes offer excellent compatibility with a wide range of substances and processes. They can transport various fluids and gases, including corrosive chemicals, hydrocarbons, and high-temperature steam. The versatility of nickel alloy tubes makes them suitable for diverse applications across industries, ranging from heat exchangers and condensers to downhole equipment and refinery processing units.
Manufacturers and engineers have embraced nickel alloy tubes for their exceptional performance and reliability. Their unique combination of corrosion resistance, heat resistance, and mechanical strength has made them a preferred choice for critical applications. Additionally, advancements in manufacturing processes and alloy development have expanded the range of available nickel alloy tubes, providing even more tailored solutions for specific industry needs.
Looking ahead, the future of nickel alloy tubes holds great promise. Ongoing research and development efforts are focused on optimizing the properties of these tubes, exploring new alloy compositions, and refining manufacturing techniques to further enhance their performance. Innovations such as improved welding technologies, advanced surface treatments, and enhanced compatibility with extreme environments are expected to drive the evolution of nickel alloy tubes, pushing the boundaries of what is possible in demanding industries.
In conclusion, nickel alloy tubes have redefined performance and reliability in industries that demand exceptional strength, corrosion resistance, and heat resistance. With their outstanding properties, including corrosion resistance, heat resistance, and mechanical strength, these specialized tubes are transforming critical sectors such as aerospace, oil and gas, chemical processing, and power generation. As industries continue to evolve, the reliance on nickel alloy tubes is expected to grow, further solidifying their position as a vital component in achieving optimal performance and reliability.
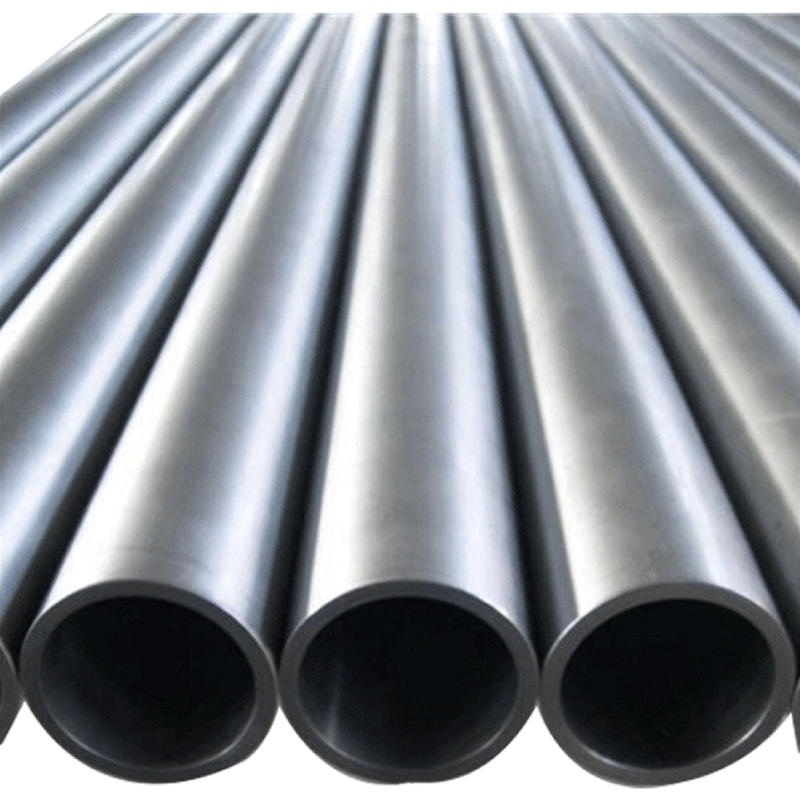
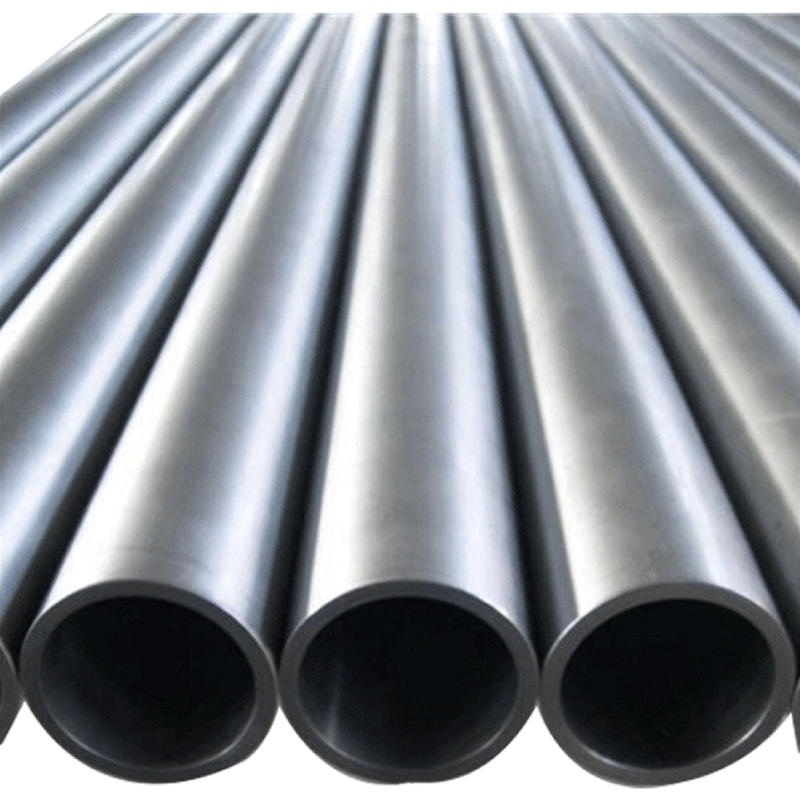