Stainless steel heat exchanger tube is used in all types of high-pressure applications. From the design engineers and fabricators to the in-plant workers who use these units on a daily basis, industry professionals constantly seek new ways to improve performance and extend unit life in corrosive environments. Specifying higher corrosion-resistant grades of tubing is one way that these challenges can be met.
Choosing the right stainless steel grade for heat exchanger tubing is crucial to ensure both long term performance and cost efficiency. Stainless steels are available in many different grades, including austenitic, duplex, ferritic, precipitation-hardenable and martensitic. All of these alloys have different strengths, hardness and corrosion resistance properties. Each has its own advantages and disadvantages depending on the application and environment in which it will operate.
The most important factor to consider when selecting a tube material is its thermal conductivity. The goal of a heat exchanger is to transfer the maximum amount of heat from the product side (usually in tubes) to the utility side (typically in the shell). The higher the conductivity, the more efficient the system. Copper and copper/nickel are the most conductive of all tube materials, followed by carbon steel and then stainless steel.
In addition to its conductivity, stainless steel has a low coefficient of thermal expansion across the temperature range in which it operates. This allows the tube to be thinner than other metals, which reduces the pressure and cost of a heat exchanger. It also helps reduce thermal stresses, which can cause cracking of the tube.
These stresses can be caused by thermal cycling, vibrations and shocks. The most common source of stress is thermal cycling. A tube that has been subjected to repeated cycles of high temperatures and lower temperatures will develop a pitting, corrosion fatigue or stress corrosion cracking (SCC) defect on the surface of the tube.
This damage is usually caused by the interaction of oxygen and chloride ions with the surface of the tube. It can also be caused by the presence of other trace elements such as magnesium, silicon, phosphorus and nitrogen.
We can provide welded heat exchanger tube in any size, length and thickness, bright annealing pickling, or cold drawn, controlled tolerance of outside diameter, wall thickness and hoop strength. We are committed to providing a high level of quality for our customers. Our heat exchanger tube is tested for tensile strength and mechanical properties, including hardness and flattening. We can also provide our customers with a full set of non-destructive testing services including magnetic particle inspection, eddy current and ultrasonic inspection. Contact us to find out how we can meet your specifications for stainless steel heat exchanger tube.
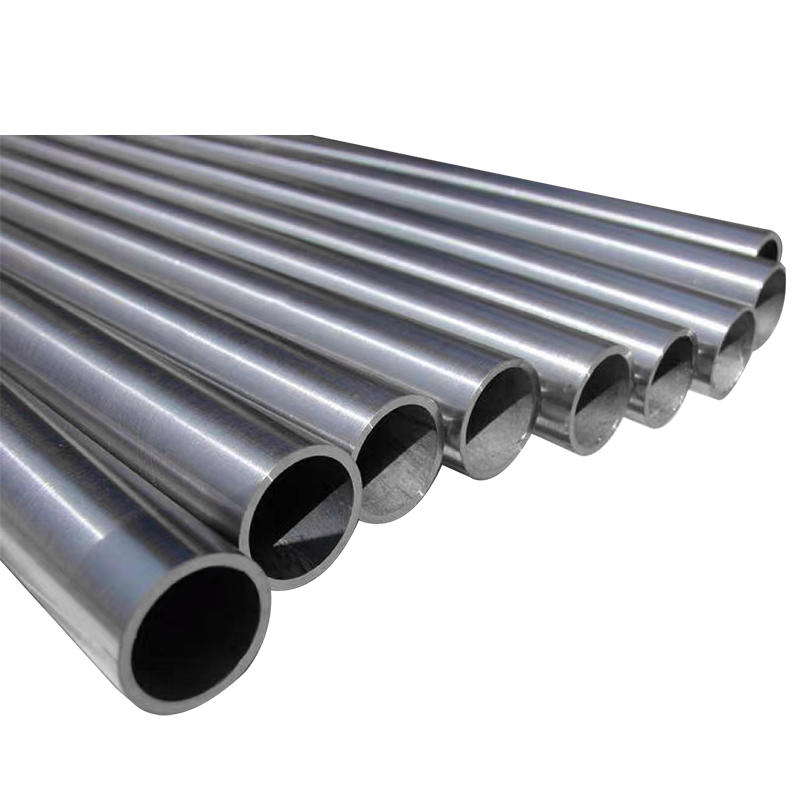
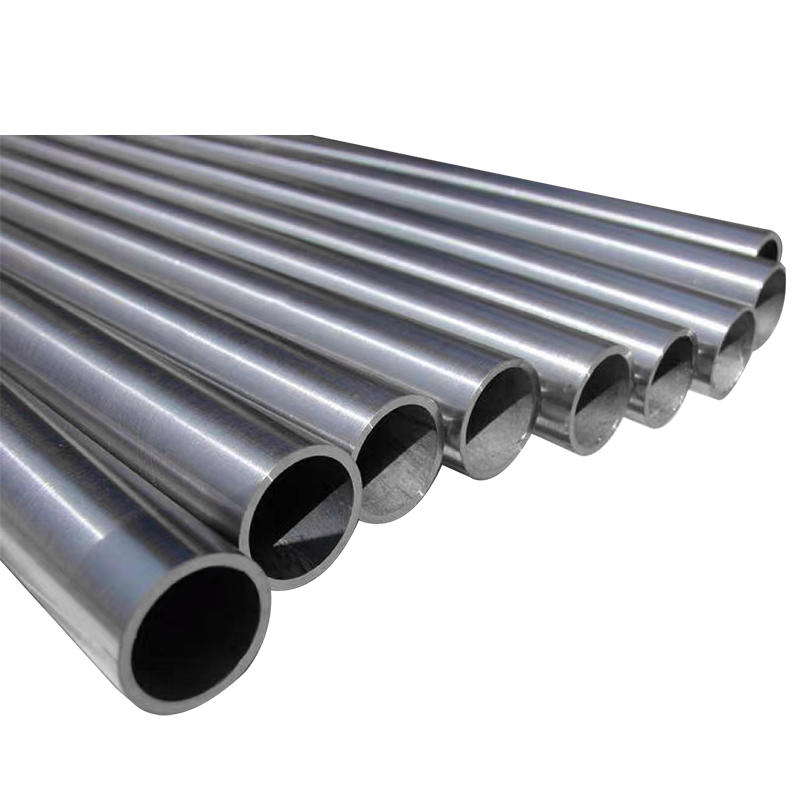