A versatile product, stainless steel tube can serve a range of industries with its many applications. From conveying corrosive or non-corrosive liquids to withstanding hot or cold gases and liquids, stainless steel tubing has proven itself useful to both engineers and architects. Being extremely flexible metal it comes in all sizes from miniature hypodermic tubing up to pipes for industrial uses - perfect for all engineers and architects!
Structural stainless steel tubing is a go-to choice for builders and manufacturers due to its strength, corrosion resistance, low maintenance costs, and precision sizing based on outside diameter and wall thickness - giving rise to various tubing types including fractional, hypodermic, square, and metric sizes.
When purchasing tubing for certain applications, fabrication processes, and finishing methods must also be considered. This is especially relevant when purchasing sanitary tubing that will be used in food, pharmaceutical, or medical facilities that must adhere to high levels of cleanliness standards in their operations and processing. Fabricators therefore face increasing pressure to minimize downtime while creating lean efficiencies to meet tight tolerances and specifications while meeting customer demands.
Since stainless steel tubing in high-visibility environments requires a flawless outer diameter finish, increasing attention has been focused on its finishing. To meet this demand, CS Unitec is expanding its line of power tools and grinding/polishing disks to address it. "Customers now expect hairline to mirror finishes on their tube instead of just brush finishes," according to Tom Carroll, President of CS Unitec.
These tube finishes can be achieved through rolling, drawing, sanding, or bead blasting to remove weld beads and defects on both ID and OD surfaces. Once desired surfaces have been reached, tubing can then be polished for traceability purposes or manufacturer identification purposes before being stenciled to identify its maker.
Although the stainless steel tubing industry is highly automated, its production involves numerous variables that could impact its quality. For example, the type of metallurgy used can significantly influence how well the finished product responds to stress and corrosion.
Austenitic grades 316 or 316L tubing may experience stress corrosion cracking known as pitting or crevice corrosion, caused either by environmental stressors or defects within the tube itself. When exposed to stress events, gas may be released causing small pits on its outer diameter surface (OD) surface that appear like mushroom-shaped marks visible by naked eye.
Drawn-over-mandrel (DOM), is an effective tubing finishing solution. In the manufacturing process, tubes are passed over a smaller mandrel than itself - giving the tubing extra support and preventing unwanted wrinkles. Furthermore, this process also enables tight tolerances and precise sizing through this precision method.
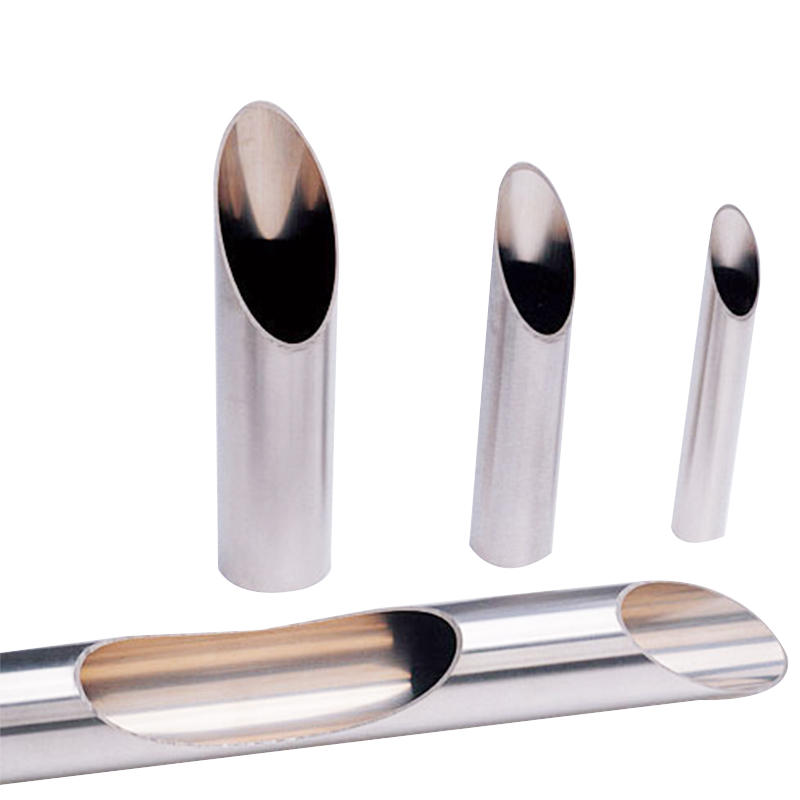