In most industrial applications, stainless steel tubing is required to operate in harsh environments. These conditions can cause the material to oxidize quickly. The bright annealing process reduces this oxidation, improving the corrosion resistance of the tube. It also gives it a shiny appearance. In addition, this type of annealing reduces the surface hardness of the tube, making it easier to weld and machine.
In the United States and much of Europe, bright annealing is the standard method for annealing tubing. After annealing, the tubing is usually mechanically polished to 180-240 grit on both the OD and ID. This enables the tube to be used in a variety of applications, including in chloride (salt water) environments.
Bright annealing is an important step in the production of high quality stainless steel tubing. The main goal is to remove the work hardening that causes the tube to oxidize rapidly. This can be done in a furnace with a protective atmosphere. The protective atmosphere is a nitrogen rich, carbon free gas with a low dew point. The furnace is also equipped with an inlet and outlet sealing box to prevent the ingress of oxygen and moisture.
The inlet and outlet seals of the furnace should be a few parts per million tight. They ensure that the nitrogen rich, carbon free atmosphere is sealed tightly so that oxygen and water vapor cannot enter and the protective atmosphere can’t escape. The atmosphere should also be monitored closely for carbide precipitation at grain boundaries. The austenitic stainless steel products should be annealed at a temperature higher than the austeniteizing temperature and cooled rapidly to avoid carbide precipitation.
Another important reason to use bright annealing is that it reduces the need for pickling. Pickling can damage the internal surface of the tubing and cause pitting corrosion. This can be very dangerous and costly for the customer in many cases. Bright annealing is much safer because it does not remove the protective oxide layer.
In order to ensure the quality of the bright annealing process, the furnace should be controlled carefully. The reducing gas should be a low dew point, carbon free and odorless. The tube should be continuously withdrawn and tested for carbon free nitrogen and low dew point. In addition, the temperature of the annealing furnace should be monitored.
In addition to this, a stainless steel continuous bright annealing line should have the ability to accommodate virtually any line speed, product dimension and material- supporting oxygen-free copper, brass, nickel, titanium, and more. They can even be equipped with payoffs, straighteners, drives and reel to reel offline processing. This makes them the preferred choice for lean, agile manufacturing. Contact a Radyne sales engineer today to learn more about this new technology. We’re here to help you find the best solution for your specific application.
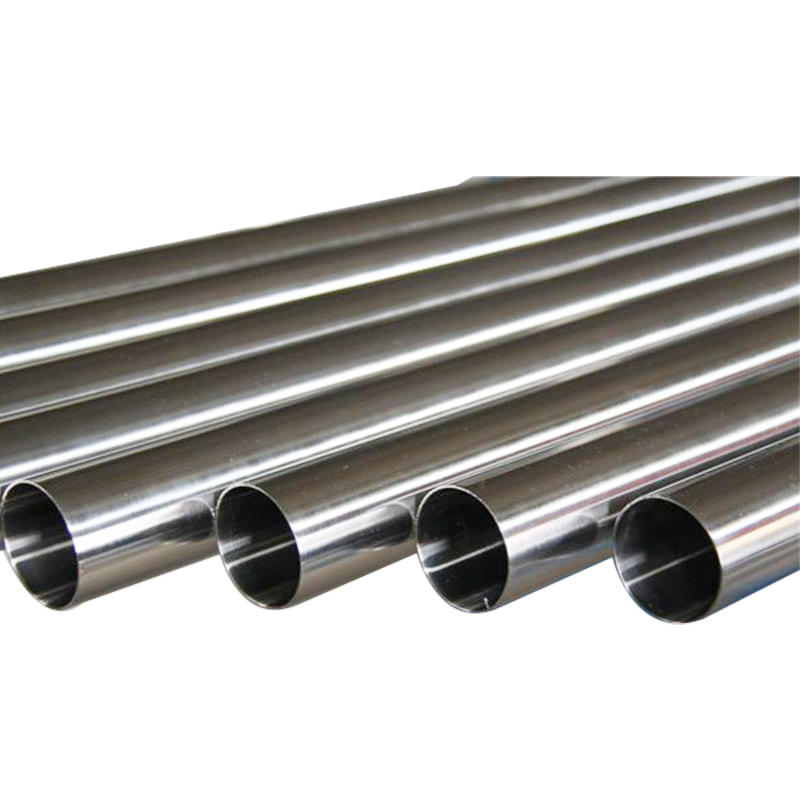