Stainless steel EP tubing is used in a wide variety of industrial and medical applications. These tubes are incredibly durable and resist corrosion, making them ideal for high-pressure or corrosive environments. They are also highly versatile, allowing them to be bent or curved to suit specific requirements. The EP process significantly improves the surface of the stainless steel tubing, which reduces friction and provides a more smooth, hygienic finish. In addition to this, the EP process removes impurities that can cause contamination in pharmaceutical, food and beverage applications.
EP is an electrochemical process that refinishes stainless steel tubes to a high degree of cleanliness and brightness. Its effectiveness is attributed to its ability to eliminate pores and other imperfections that can harbor bacteria, leading to the development of biofilms. These deposits are a common source of infections in healthcare facilities, but the removal of these particles by the EP process significantly reduces their likelihood of being present in the tubing system.
To achieve the EP process’s desired results, the stainless steel is immersed in an electrolyte solution that contains a phosphoric or sulphuric acid solution, along with water and other additives. During the EP process, current density is varied, which impacts the duration of the process and the amount of etching that occurs on the metal. During the etching phase, oxides and impurities are removed from the stainless steel. These oxides and impurities are responsible for corrosion and can contaminate tubing systems and other equipment. After the etching phase, chromium oxide forms on the surface of the stainless steel, which creates a passive layer that is resistant to further corrosion and impurities.
The stainless steel tubing is then rinsed with clean water to remove any remaining chemical compounds and restore the surface to its original condition. Then, the tubing is swaged to shrink its diameter at one end. This allows it to fit into a die that has been lowered to the desired length for bending. The tubing is then drawn down over the mandrel, and the pressure exerted by the drawing trolley reduces the diameter of the swagged end. Once the desired OD is reached, the mandrel is removed and the tube is cleaned to remove any residual material from the swagged end.
In an experiment that measured the lubrication capability of various materials on stainless steel EP tubing, it was found that a medium-viscosity vegetable oil with EP additives outperformed a synthetic gel, a paste, and straight petroleum in reducing scoring and tearing. In addition, this oil was more effective in preventing the adhesion of blood cells and bacteria and in improving corrosion resistance capability, surface roughness, and shine of the stainless steel. The authors of this paper suggest that the results indicate that a more appropriate EP process parameter could be developed to achieve higher corrosion resistance capabilities and to meet individual customer’s expectations.
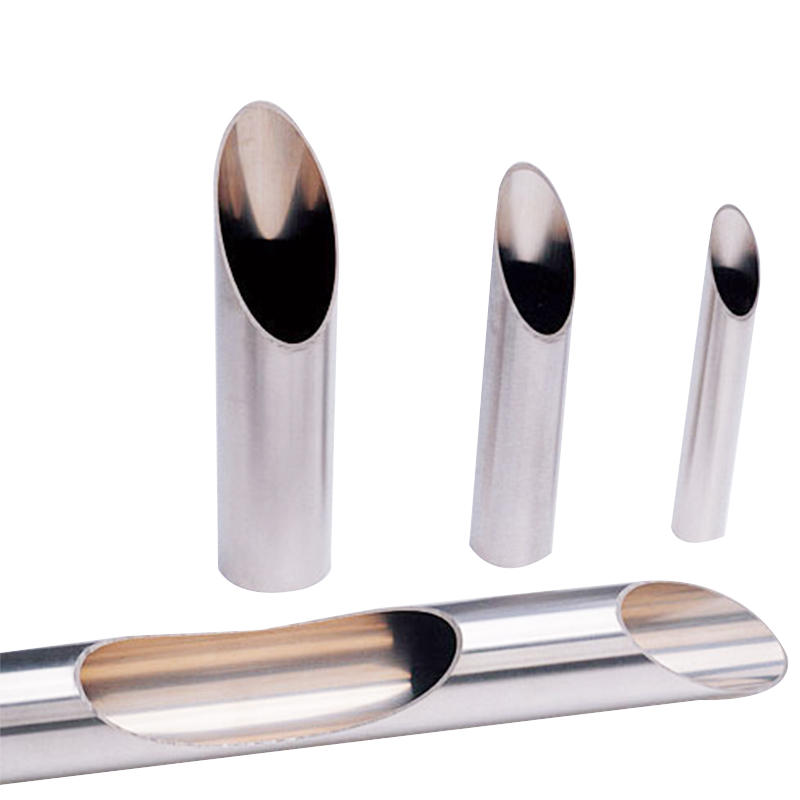
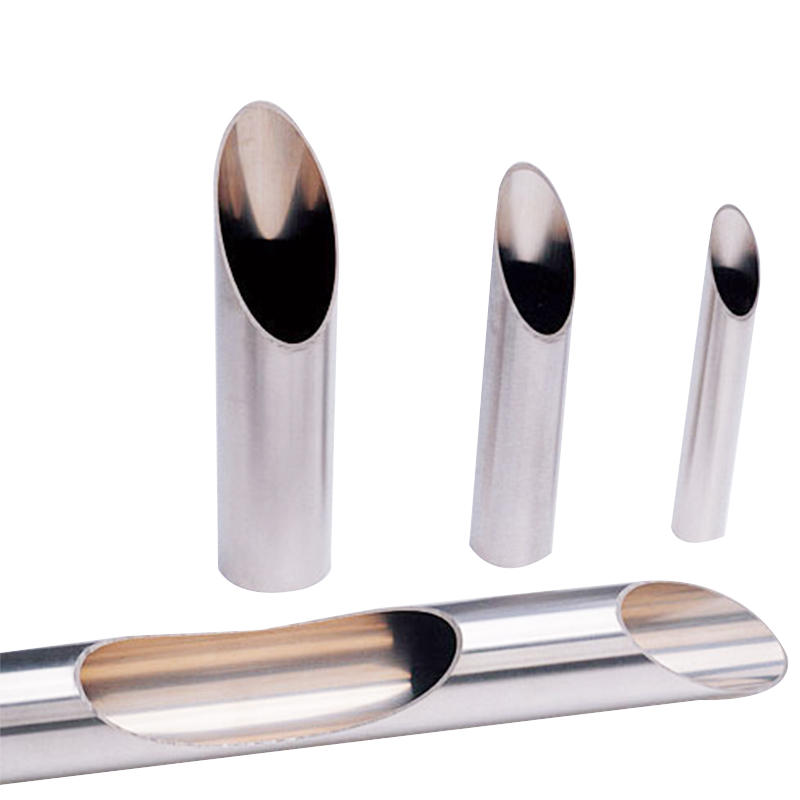