A stainless steel tube is a versatile material used in the manufacture of countless products and inventions. Its durability allows it to transport cold or hot liquids and gasses, resist deterioration from caustic chemicals and contaminants, and withstand high pressure. This makes it ideal for a wide range of industrial and commercial applications. Despite its initial cost, using a well-suited stainless steel tube in an application reduces downtime, maintenance, replacement and repair costs over the life of the product.
Stainless steel is available in a large variety of grades and alloys. The grade a fabricator selects is determined by the specific properties required. Ferritic and martensitic stainless steels are common and offer excellent corrosion resistance levels. There are also austenitic stainless steels, with higher nickel and chromium content, which provide superior resistance to corrosion.
The specific alloy selected depends on the needs of a particular tubing application. A fabricator will consider factors such as chemical resistance, temperature, mechanical properties, and cost. The tube itself may require heat-treating to achieve its desired mechanical properties. Choosing the right type of tube will help ensure a project is successful.
A common example of a critical application that utilizes stainless steel tubing is an automotive component. Stainless steel tubing is more durable than its carbon steel counterparts, making it ideal for use in automo-tive components that experience significant amounts of force and vibration. It is also lighter in weight, allowing for greater fuel efficiency. This advantage can be further enhanced by using tube hydroforming, which is becoming increasingly popular in the automotive industry, to modify a part's initial design.
The stainless steel tube comes in both welded and seamless forms. Seamless tubes have a bright finish, and are generally utilized in areas where appearance is important. Welded tube can be finished by grinding, passivation, or pickling to produce a clean surface. It is often used in sanitary and food processing applications. It is also available in a wide range of sizes and shapes, including squares, rectangles and circles.
Regardless of the application, proper welding techniques are essential. There is no voodoo when it comes to welding stainless steel, and there are many advancements that have been made in the field of pipe fabrication. Using best practices and new wrinkles on established methods allows pipe fabricators to improve productivity without sacrificing the integrity of the stainless steel tube or its corrosion resistant qualities.
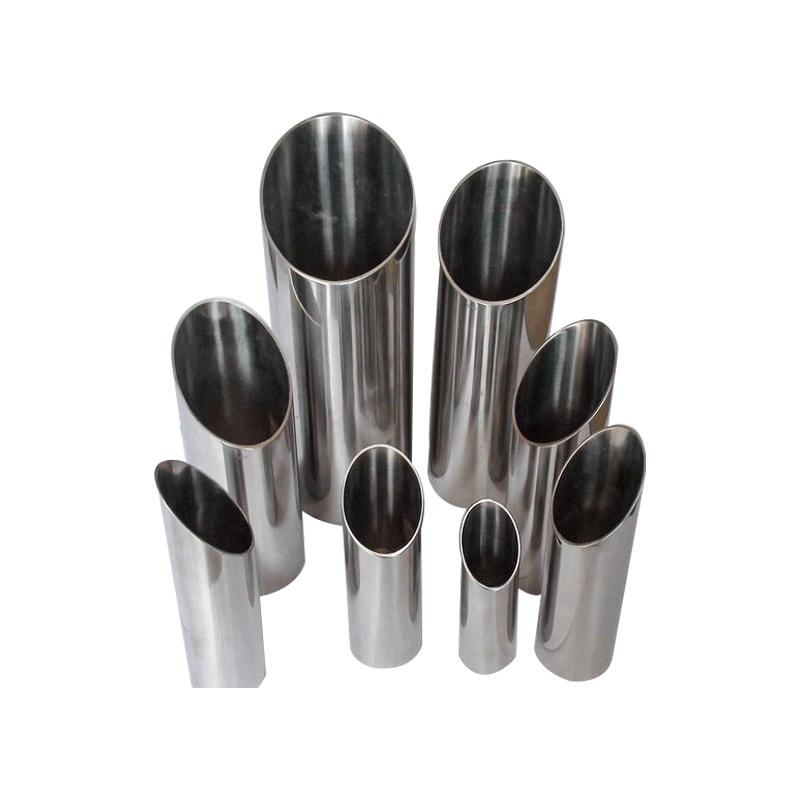